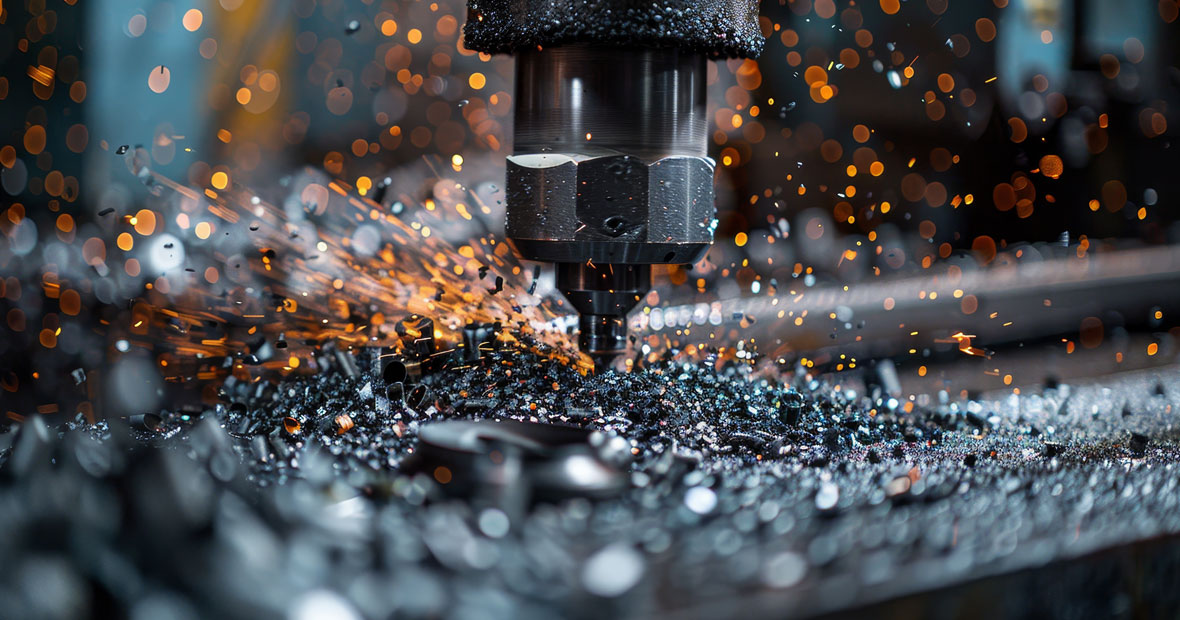
Delving into the realm of Friction Stir Welding (FSW) brings forth a multitude of complexities, especially when welding dissimilar materials. The challenge lies in overcoming material compatibility issues while optimizing process parameters to enhance joint strength. Delicate factors, including welding speed and rotation, along with the critical selection of tool shape and material, significantly influence joint quality. Thermal management emerges as another striking challenge while working with dissimilar alloys. This necessitates advanced techniques for monitoring and controlling thermal input. The quest for innovative tool designs for improving weld quality and efficiency remains a constant pursuit in this field. This discourse aims to illuminate the myriad challenges faced and the solutions currently being implemented in the fascinating world of Friction Stir Welding.
Overcoming material compatibility issues in fsw
Friction Stir Welding (FSW) presents a unique challenge when dealing with dissimilar materials. The welding of different alloys, like aluminium and steel, requires careful optimisation of FSW welding parameters to improve the junction between these dissimilar materials. Each alloy has specific requirements and characteristics that need to be tailored for successful FSW. Therefore, the selection of appropriate welding tools, designed to cater to these different alloys, becomes paramount to the success of FSW.
Advanced modeling and simulation techniques have been employed to predict the outcomes of welding between such heterogeneous materials. Studies have shown that the rotation speed and advancement have a significant impact on the quality of welding between aluminium and steel. Innovations in post-welding treatment have been introduced to enhance the mechanical strength of these dissimilar joints. One technique that has been extensively studied involves the effects of thermal homogenization on the microstructure of materials welded by FSW. By carefully regulating the heat distribution during the welding process, the inherent incompatibility between different materials can be significantly mitigated, leading to improved weld strength and durability.
Optimizing process parameters for enhanced joint strength
Within the realm of Dissimilar Materials Welding, one method stands out for its potential to create high-tensile joints between different metals : friction stir welding. This technique, reliant on a friction stir welding machine, leverages key process parameters to maximize mechanical strength and joint quality. A significant focus is the identification of these parameters, such as welding speed, rotation, and tool shape and material, which heavily influence the resultant joint strength.
Impact of Welding Speed and Rotation on Joint Quality
Understanding the correlation between the welding speed and joint quality is imperative. A modification in the speed directly influences the joints' heterogeneity and mechanical properties. Furthermore, the process's direction has a pronounced effect on the joints' durability and strength.
Importance of Tool Shape and Material in Process Optimization
Recognizing the role of tool shape and material in the welding process is paramount. The optimal penetration depth is integral to achieving maximum joint tensile strength. Pre-treatment techniques for materials are instrumental in enhancing joint strength.
Advanced Techniques for Monitoring and Controlling Thermal Input
Monitoring and controlling thermal input is another critical aspect. Post-welding cooling parameters significantly affect the strength and durability of the joints, requiring meticulous evaluation and optimization.
Addressing thermal management challenges in welding dissimilar alloys
Friction Stir Welding (FSW) of dissimilar materials presents unique challenges, notably in terms of thermal management. Recognizing the role of temperature control in welding different alloys is vital in preventing weld defects. Advanced techniques aid in maintaining an optimal temperature, thereby enhancing the quality of the welded zone. The heat diversity of the metals involved is a significant factor influencing the formation of the weld interface.
The specific challenges associated with heat dissipation in welding unlike metals are of considerable concern. Strategies are in place to optimize the welding process, aiming to balance the thermal flows between the different alloys. One method adopted is the use of numerical simulations. These simulations provide a means to predict and improve thermal management in welding dissimilar metals, enabling a more effective and efficient process.
Innovative tool design for improved weld quality and efficiency
In the realm of Friction Stir Welding (FSW) of dissimilar materials, constant advancements continually redefine the scope of quality and efficiency seen in the field.
stands as a testament to this progress. The evolution of pin designs, for instance, has played a significant role in optimizing the quality of welds in dissimilar joints. The geometry of the tool's shoulder significantly impacts the efficiency of the friction welding process, with the correct proportions leading to enhanced results.
Advanced materials employed in tool creation further bolster the durability and performance of welds, ultimately offering improved longevity and reliability. Adaptive control techniques present a real-time adjustment of tool parameters, thereby ensuring high-quality joints. By integrating cooling systems within tool design, welding defects become preventable, leading to an overall improvement in the quality of the welds. The development of multi-tool solutions has been instrumental in accelerating the joining of dissimilar materials without compromising on joint quality. These innovations present a bright future for the welding industry, promising unprecedented quality and efficiency in every weld.